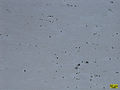
Highlander 613™
Image of Highlander 613 @ 50X
Generated in-house
.jpg)
Why Scot Forge Forges Highlander 613™ Aluminum Alloy (A96013)
During collaborative discussions with industry experts, a recurring deficiency was noted for forged aluminum products, the need for aluminum with excellent fatigue endurance, toughness and corrosion resistance characteristics.
Scot Forge worked with these experts to perform a study evaluating suitable aluminum alloy compositions capable of meeting the strict criteria for forged components used in Naval, Aerospace and Defense applications. The results lead to the development of an alloy, aluminum 6013, that when tempered is well adapted for many forging applications.
Aluminum Comparison Chart
Aluminum 6013 (A96013) Provides Fatigue Endurance, Toughness and Corrosion Resistance.
.png)
HIGHLANDER 613™ IS ALREADY BEING USED FOR COMPONENTS IN:
Fall pipe
Subsea Remotely Operated Vehicles (ROVs)
Naval weapons systems
Commercial submarines
Mold-making equipment
National laboratory experimental programs
Missile and fire control systems
Plastic/blown film molding equipment
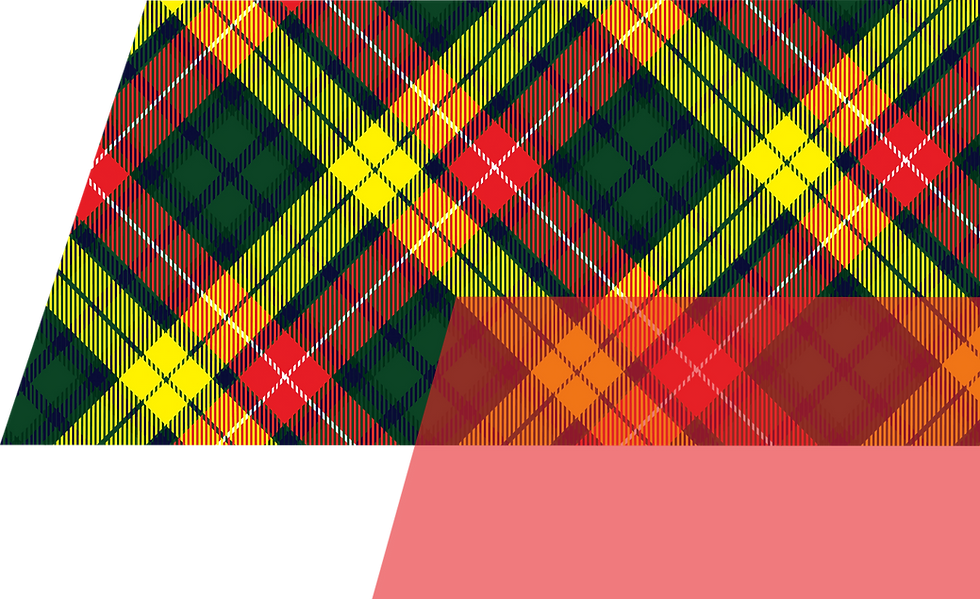
Development of Highlander 613™
Scot Forge has devised a proprietary processing method for this aluminum 6013 and dubbed it Highlander 613™. Originally Highlander 613™ was developed as a better alternative to the traditionally forged alloy 6061 but, after reviewing and optimizing the material’s forging properties, we have also found it to present substantial benefits when compared aluminum alloys of the 7XXX and 2XXX series as an all-around versatile product.
Highlander 613™ Comparison of Material Properties
Highlander 613™ has demonstrated significantly enhanced corrosion resistance properties and is virtually immune to stress corrosion cracking. Its fracture toughness and fatigue resistance exceed many of the other 2XXX, 6XXX and 7XXX series alloys while echoing the excellent machinability of 2XXX and 7XXX series. Highlander 613™ also outperforms many of the other aerospace alloys at elevated temperatures, exceeds stress rupture properties and has superior brazeability. Additionally, Highlander 613™ can be welded by conventional means and is impervious to hot cracking during welding, whereas the alloys of the 7XXX series cannot and are not.
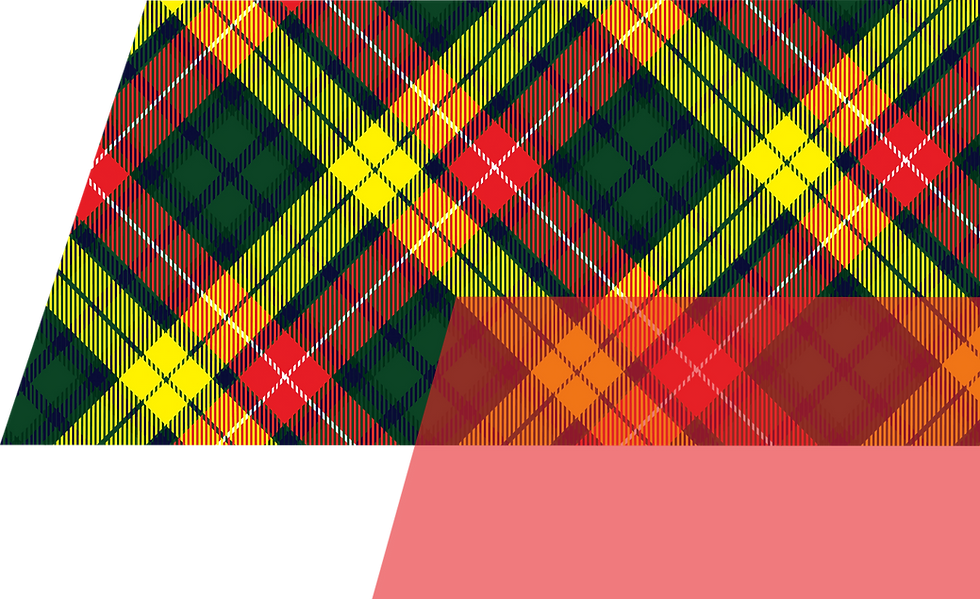
Scot Forge Difference
At Scot Forge, we know the importance of getting your parts on-time, as expected. However, for customers new to procuring forgings, ordering a forging that will meet all specifications for end-use applications may be a challenge, which is why finding a trusted supplier and partner is essential. Our employee-owners are here to ensure your project stays on track with our forgings by offering:
Quality Assurance
Scot Forge is proud to be ISO 9001:2015 and AS9100D certified, and our team is committed to providing outstanding customer satisfaction. Further pursuance of aerospace products has led to NADCAP accreditation in both Heat Treatment for nickel material and Nondestructive Testing.
Every Scot Forge customer gets placed with a qualified team that will guide each nickel forging delivered from the inquiry stage to order placement, expediting and shipping.
We offer many size forgings in both standard and unique geometries to meet your needs.
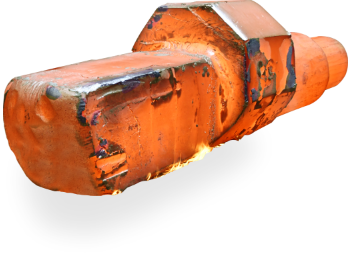
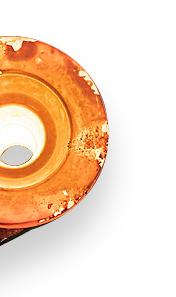