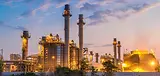
FORGING POWER GENERATION
.jpg)
Future Of Energy - Forging In Motion
The Scot Forge Power Generation Services Team provides timely solutions our customers. From simple rings to complex shapes with geometries that push the envelope of open die forging, we have the in-house capabilities to manufacture a variety of power generation components that meet your most stringent requirements. Our industry specialists, along with our forging and metallurgical teams, provide world-class program management from initial contact to project completion.
Power Generation Expertise
The power generation industry is highly technical and requires forged parts that are robust and can endure prolonged exposure to extreme temperatures, wind, saltwater, environmental factors and various chemicals. Forged parts for the power generation industry are commonly manufactured through the open die forge process from stainless steel and different copper alloys. Find our forgings in:
Nuclear - Used in critical applications for containment and storage
Oil & Gas - Trusted to protect the environment
Marine Propulsion - Relied upon for mission-essential functions
Power Generation Forged Parts
Forged shapes for turbines, generators, compressors, gear boxes, heat exchangers and blowers:
Forged shapes for turbines, generators, compressors, gear boxes, heat exchangers and blowers:
Hollows: Reactor Pressure Vessels (RPVs), Boiling Water Reactors (BWRs) and Small Modular Reactors (SMR)
Rings (Full/Segmented): Diaphragms, stators, spacers, retainers, motor ends, shear resistances, locks, seals, adapter or spherical seats, flanges and sleeves
Shafts: Rotors, generators, turbines, suction/discharge end stubs, couplings, valve stems and fans
Discs and Hubs: Covers, wheels, suction/discharge end caps, adapters, impellers, tube sheets and nozzles
Complex Shapes: Bucket/fan blade stock and turbine blades
Additional Shapes: Casings, spacers, centrifuge bowls, bearing blocks, shells and transition cones
HISTORY OF FORGING & POWER GENERATION
Generating electricity traces back to the Greeks, with significant milestones during the 1800s with the first wind turbine and variations of wires and magnets to create electrical currents. Then, with the commercialization of electrical production in the 19th Century, new methods to produce electricity came about. These methods include steam engines, which became widely used to provide electricity, including coal-fueled boilers that provided power to operate boats and trains; nuclear energy was beginning to emerge with the development of nuclear fission. As a result, electricity became more readily available, and public buildings and businesses could have electricity. Around 1965, we were using Nuclear, hydropower and Oil & Gas to produce power in addition to traditional biomass, such as wood or charcoal. From 1990 to today, power generation continues to be an evolving industry with wind, solar and modern biofuels coming onto the scene. As new technology and energy sources power our world, we at Scot Forge are prepared to support them. From large spindles for wind turbines to step shafts for two-pole generator forgings. We look forward to overcoming the challenges facing renewable energy, such as energy storage, and embracing the opportunities for innovation, such as small modular reactors or off-shore wind, as the power generation sector continues to grow.
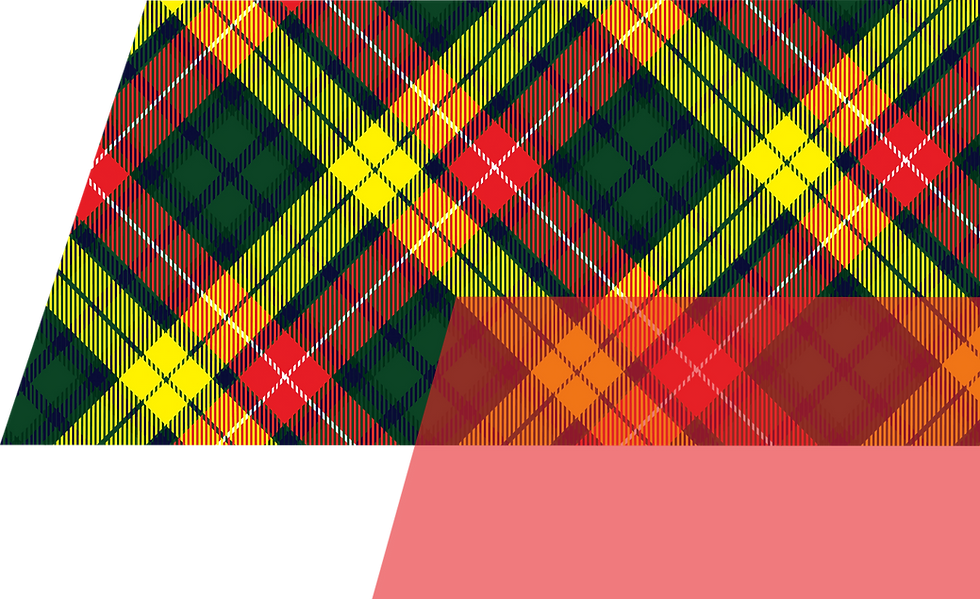
On-Time Delivery - Our Priority
With a long history of working in the industry, we understand how crucial on-time delivery can be. The Scot Forge Power Generation Services Team is well-versed in the pre- and post-award requirements, from material-process plans to NDE procedures. We know the right steps to take in order to deliver your product on time.
Emergency Response
Our Power Generation Services Team knows that in times of unplanned outages or critical situations, thousands—if not millions—of dollars can be lost each day. As a result, we have established an emergency response program that allows for daily entry of breakdown and rush orders for immediate production response.
A Vast Inventory of Materials
We maintain an extensive inventory of ferrous and non-ferrous materials and can quickly provide vacuum degassed air melt, ESR or VAR for improved cleanliness levels. Our parts are supplied using the highest-quality material available. Power generation-specific materials include carbon, alloy, stainless steel, copper base, nickel base and custom-melt alloys that meet OEM specifications.
Flexible Sizes, Shapes and Quantities
No matter the grade of material or shape and size of the part, our facilities are designed to support both single-piece and high-volume manufacturing.
Questions? Contact a Forging Expert
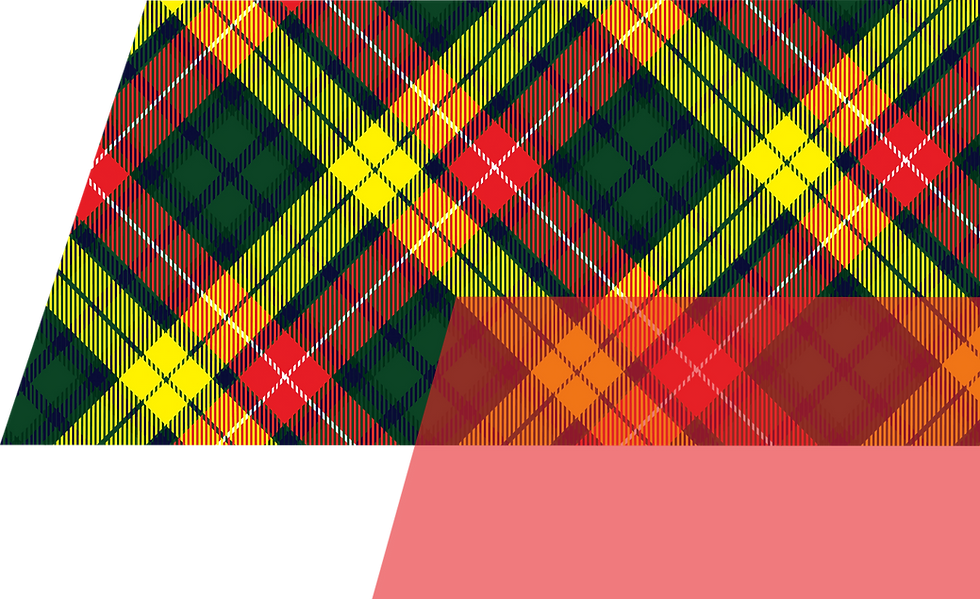
Scot Forge Difference
At Scot Forge, we know the importance of getting your parts on-time, as expected. However, for customers new to procuring forgings, ordering a forging that will meet all specifications for end-use applications may be a challenge, which is why finding a trusted supplier and partner is essential. Our employee-owners are here to ensure your project stays on track with our forgings by offering:
Quality Assurance
Scot Forge is proud to be ISO 9001:2015 and AS9100D certified, and our team is committed to providing outstanding customer satisfaction. Further pursuance of aerospace products has led to NADCAP accreditation in both Heat Treatment for nickel material and Nondestructive Testing.
Every Scot Forge customer gets placed with a qualified team that will guide each nickel forging delivered from the inquiry stage to order placement, expediting and shipping.
We offer many size forgings in both standard and unique geometries to meet your needs.
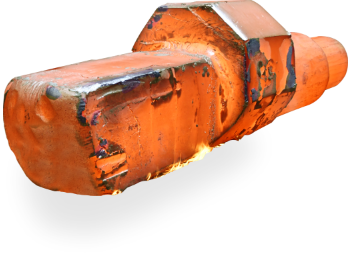
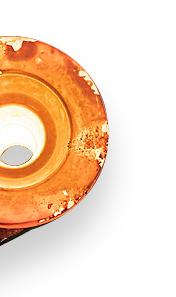